Understanding ABS Injection Molding Temperature for Optimal Plastic Production
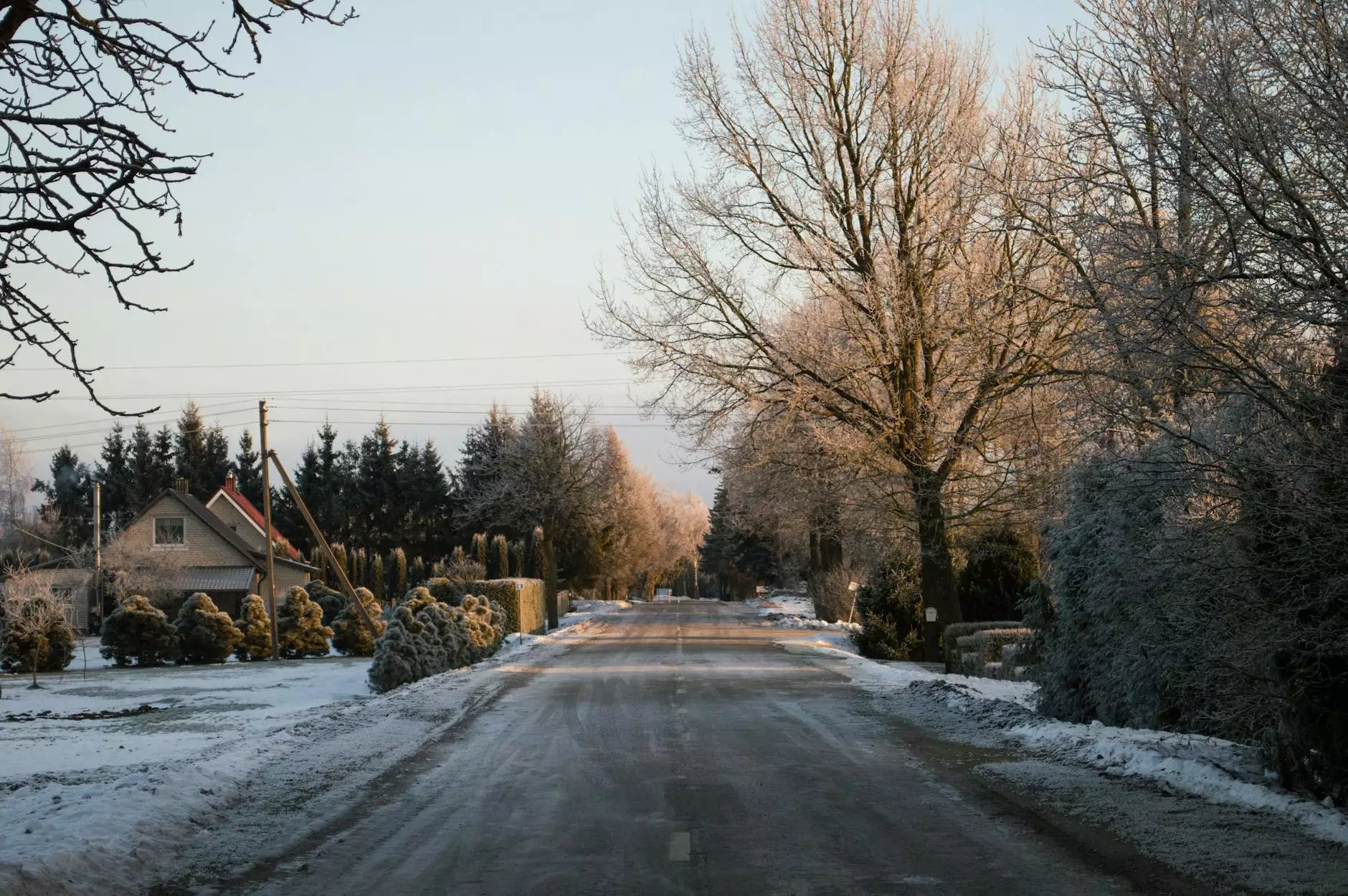
In the realm of plastic manufacturing, especially in the field of injection molding, understanding the intricacies of temperature control is paramount. One of the most significant polymers utilized in the injection molding process is Acrylonitrile Butadiene Styrene (ABS). This article delves into the ABS injection molding temperature and its influence on the overall quality and success of the molded products.
What is ABS and Why is Temperature Important?
ABS is a thermoplastic polymer known for its toughness, impact resistance, and strength. It is widely used in various industries, including automotive, consumer goods, and electronics. The thermal properties of ABS make it essential to control the temperature during the injection molding process. Proper temperature management ensures:
- Optimal melt flow: Ensuring the ABS material flows adequately into the mold.
- Surface finish: Achieving a smooth and aesthetic appearance on final products.
- Dimensional stability: Producing parts that meet precise specifications.
- Reduced defects: Minimizing issues like warping, sinking, and surface blemishes.
The Ideal Temperature Range for ABS Injection Molding
Determining the ABS injection molding temperature is crucial for achieving the desired results. The optimal temperature range for ABS injection molding is typically between 190°C and 250°C (374°F to 482°F). This range can vary based on several factors, including:
- The specific grade of ABS being used.
- The complexity of the part being manufactured.
- The configuration of the injection molding machine.
Factors Influencing the Molding Temperature
Several factors must be considered when setting the injection molding temperature for ABS:
1. Material Grade
Different grades of ABS may require variations in processing temperatures. Standard grades may mold well within the typical range, while specialty grades might necessitate adjustments.
2. Part Design and Complexity
Complex parts with intricate designs often require a higher temperature to ensure complete filling of the mold and to avoid issues like short shots or incomplete parts.
3. Machine Capabilities
The performance of your injection molding machine can greatly affect temperature settings. Machines equipped with advanced temperature controls may allow for more precise adjustments.
The Impact of Too Low or Too High Temperatures
Improper temperature settings can lead to various manufacturing issues:
Low Temperature Issues
- Blocked Flow: If the temperature is too low, the ABS may not flow well, resulting in incomplete fills and part defects.
- Increased Viscosity: Lower temperatures increase material viscosity, making it harder to inject the material into the mold.
High Temperature Issues
- Degradation: Excessively high temperatures can cause thermal degradation of ABS, leading to discoloration and a decrease in mechanical properties.
- Increased Production Time: Higher temperatures can also cause longer cooling times, affecting the overall efficiency of the production cycle.
Optimizing Your Injection Molding Process
To achieve the best results when working with ABS, consider the following optimization strategies:
1. Conduct Material Testing
Before commencing full-scale production, it is beneficial to perform material testing to determine the optimal molding temperatures for different grades of ABS.
2. Monitor Processing Conditions
Regularly monitor the temperature during the injection molding process to ensure consistency. Use accurate thermocouples and PID controllers to maintain the desired thermal environment.
3. Adjust Cooling Times Accordingly
Based on the molding temperatures and material properties, adjust the cooling times to ensure that parts are adequately cooled without causing warping or defects.
Leveraging Technology in Temperature Management
Modern technology can significantly enhance the management of ABS injection molding temperature. Innovations include:
Automated Thermoregulation Systems
Automated systems can monitor and adjust temperatures in real-time, providing a more stable and controlled environment for the injection process, thereby improving product quality.
Simulation Software
Utilizing simulation software before production can help manufacturers visualize how temperature settings will affect the flow and cooling of ABS, leading to better-informed decisions.
Case Studies: Successful ABS Injection Molding Practices
Let’s explore some successful implementations in ABS injection molding that highlight the importance of managing temperature.
Case Study 1: Consumer Electronics
A well-known consumer electronics manufacturer implemented stringent temperature controls in their ABS injection molding processes, resulting in enhanced part precision and a 15% reduction in material waste. By maintaining temperatures within optimal ranges, they significantly improved their production efficiency and product reliability.
Case Study 2: Automotive Parts
An automotive parts supplier used advanced temperature management systems to address previous quality issues attributed to temperature inconsistencies. By stabilizing the molding temperatures, they achieved a 20% increase in product acceptance rates during quality inspections.
Conclusion
Optimizing the ABS injection molding temperature is crucial for any plastic mold maker and manufacturer. Understanding the material properties, utilizing technology for precise temperature control, and continuously monitoring the injection process are vital steps in achieving excellence in plastic production.
As businesses prioritize quality and efficiency, focusing on the nuances of temperature management will ensure that manufacturers like Hanking Mould remain competitive in the burgeoning plastic industry.
For more information on becoming a leading plastic injection mould manufacturer or for consulting services regarding ABS injection molding practices, visit hanking-mould.com.