Exploring the Benefits of Silicone Membrane for Vacuum Forming
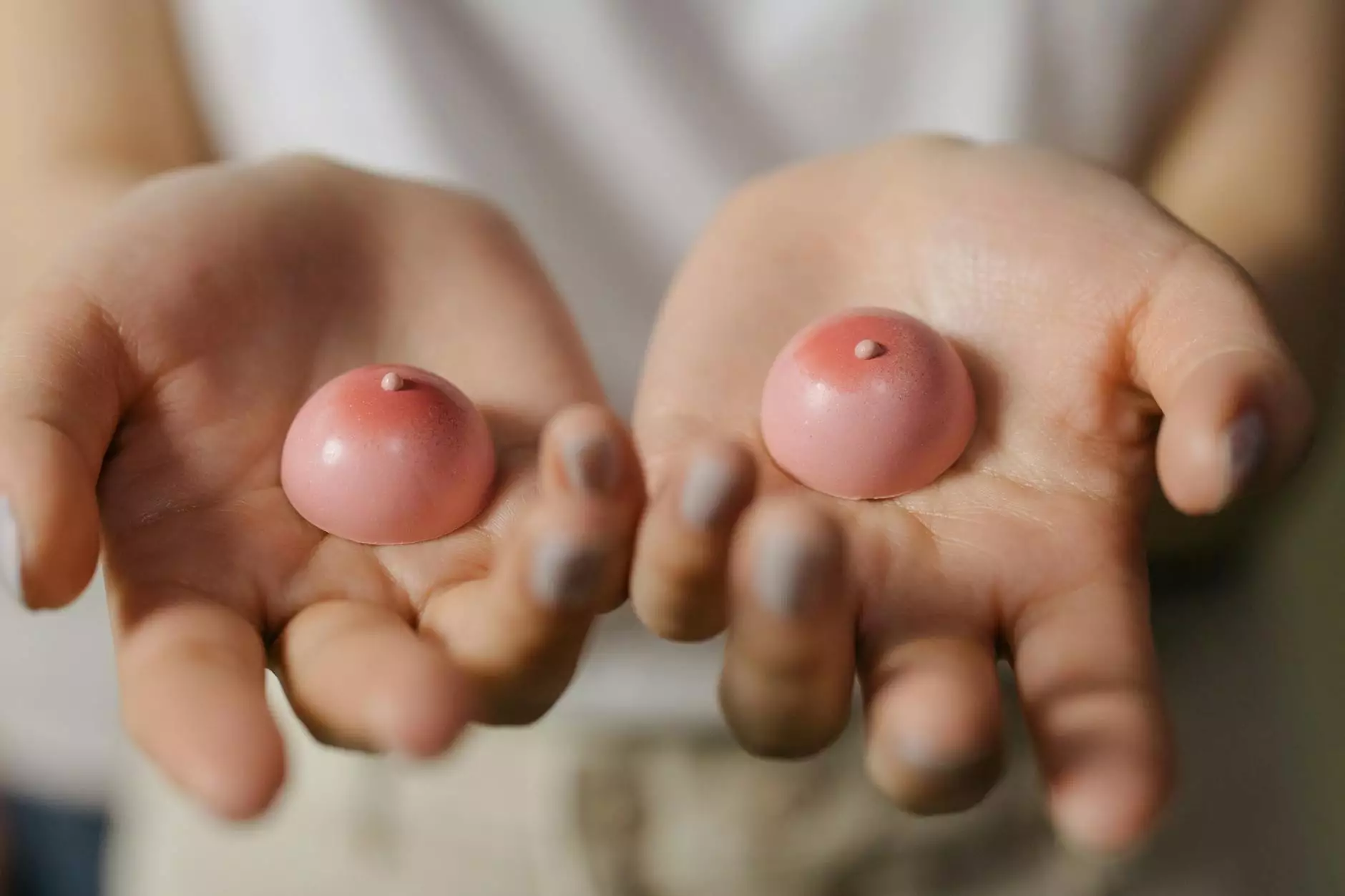
In the realm of industrial manufacturing, silicone membranes play a pivotal role, especially in vacuum forming applications. These versatile materials provide distinct advantages that enhance the efficiency, quality, and sustainability of various production processes. In this article, we will delve into the exciting world of silicone membranes, their numerous benefits, and why they are becoming an indispensable component for businesses worldwide, including the essential offerings at vacuum-presses.com.
What is Vacuum Forming?
Vacuum forming is a manufacturing process that involves heating a plastic sheet and then shaping it over a mold using vacuum pressure. This technique is widely utilized across various industries, including automotive, packaging, and consumer goods. The process is efficient and allows for the rapid production of intricate shapes and designs.
The Role of Silicone Membranes in Vacuum Forming
In vacuum forming, the role of the silicone membrane is essential. It acts as a flexible layer that aids in creating a tight seal between the heated plastic sheet and the mold surface. The properties of silicone make it an ideal choice for this application. Here are some of the reasons why:
- Temperature Resistance: Silicone membranes can withstand high temperatures, allowing for effective use in various heating conditions during the vacuum forming process.
- Durability: Silicone is highly resistant to wear and tear, ensuring a longer lifespan for the membranes, even under repeated cycles of use.
- Flexibility: The inherent flexibility of silicone makes it easier to conform to complex mold shapes, ensuring a uniform distribution of pressure that results in a better final product.
- Non-Stick Surface: Silicone materials exhibit non-stick properties, which facilitate easy removal of the formed product without damaging either the product or the mold.
Advantages of Using Silicone Membrane for Vacuum Forming
Transitioning to the use of silicone membranes in vacuum forming processes comes with several notable benefits:
1. Enhanced Product Quality
The precision that silicone membranes bring to vacuum forming can significantly improve the quality of the end product. By conforming closely to the mold, they minimize imperfections, ensuring that products have smoother surfaces and more accurate dimensions.
2. Cost-Effectiveness
Although the initial investment in silicone membranes might be higher compared to other materials, their durability and longevity result in lower replacement costs over time. Additionally, the enhanced product quality can lead to fewer reworks and higher yield rates, ultimately saving manufacturers significant amounts in operational costs.
3. Environmental Benefits
Companies are increasingly aligning their operations with sustainability goals. Silicone membranes are often produced using eco-friendly processes and are more environmentally stable than other types of membranes, such as those made from rubber or plastic. Their extended lifespan also reduces waste, contributing to a greener manufacturing approach.
4. Versatility in Applications
Silicone membranes are not only limited to vacuum forming; they offer versatility and can be utilized for various applications, including:
- Pneumatic devices
- Medical equipment
- Food packaging
- Custom mold making
Key Considerations When Choosing Silicone Membrane
When selecting a silicone membrane for vacuum forming applications, several factors should be considered:
1. Thickness and Hardness
The thickness and hardness of the silicone membrane can affect its performance significantly. Thicker alternatives might offer added durability, while softer membranes might provide better flexibility for intricate molds.
2. Temperature Resistance
Ensure that the silicone membrane can withstand the specific temperatures involved in your vacuum forming processes. Different silicone compounds offer varying degrees of temperature resistance, which is critical for the overall reliability of the forming process.
3. Compatibility with Materials
It’s crucial to ensure that the silicone membrane is compatible with the types of plastic or materials being used in the vacuum forming process. Some materials may react with certain silicone compounds, leading to contamination or degradation of the membrane.
Applications of Silicone Membranes in Various Industries
The application of silicone membranes for vacuum forming is prevalent across a wide range of industries:
1. Automotive Industry
In the automotive sector, silicone membranes are used for forming components such as dashboards, panels, and covers that require durability and flexibility, ensuring that the final products meet stringent standards for performance and aesthetics.
2. Consumer Goods
From packaging to custom-shaped items, silicone membranes help shape products that are not only functional but also appealing to consumers. Their use in creating intricate designs adds value and appeal to the final merchandise.
3. Medical Sector
In the medical industry, the accuracy and cleanliness of the molded products are paramount. Silicone membranes reduce the risk of contamination and can be sanitized, making them an ideal choice for medical devices and components.
4. Food Packaging
Silicone’s non-toxic properties make it suitable for use in food production and packaging. Manufacturers utilize silicone membranes to create custom food packaging solutions that enhance product preservation while maintaining safety standards.
Buying Options at Vacuum-presses.com
At vacuum-presses.com, we offer a comprehensive selection of silicone membranes and various related products designed for vacuum forming:
1. Buy Membranes
Our collection of silicone membranes are tailored to meet diverse requirements of manufacturers looking for quality and reliability. We ensure that our products pass stringent quality tests, granting you confidence in your choice.
2. Rubber Membranes
For those in need of alternatives, our range includes durable rubber membranes suitable for specific industrial applications, providing flexibility and resilience.
3. Vacuum System Parts
Comprehensive solutions extend beyond membranes to include vital components of vacuum systems, allowing you to source everything necessary for an efficient setup.
4. Natural Rubber Membranes
Our natural rubber membranes are supplied alongside high-quality silicone options, catering to different manufacturing needs while ensuring environmental sustainability.
Conclusion
The future of manufacturing is about efficiency, quality, and sustainability, and utilizing silicone membranes for vacuum forming embodies these principles. With their range of benefits—from enhanced product quality to environmental advantages—silicone membranes are a vital asset in various industrial applications. To explore our extensive range of silicone membranes and other vacuum system products, visit vacuum-presses.com today.
Choosing the right membrane can make a significant difference in your production processes, so consider investing in silicone membranes that promise durability, flexibility, and superb performance for your vacuum forming needs.